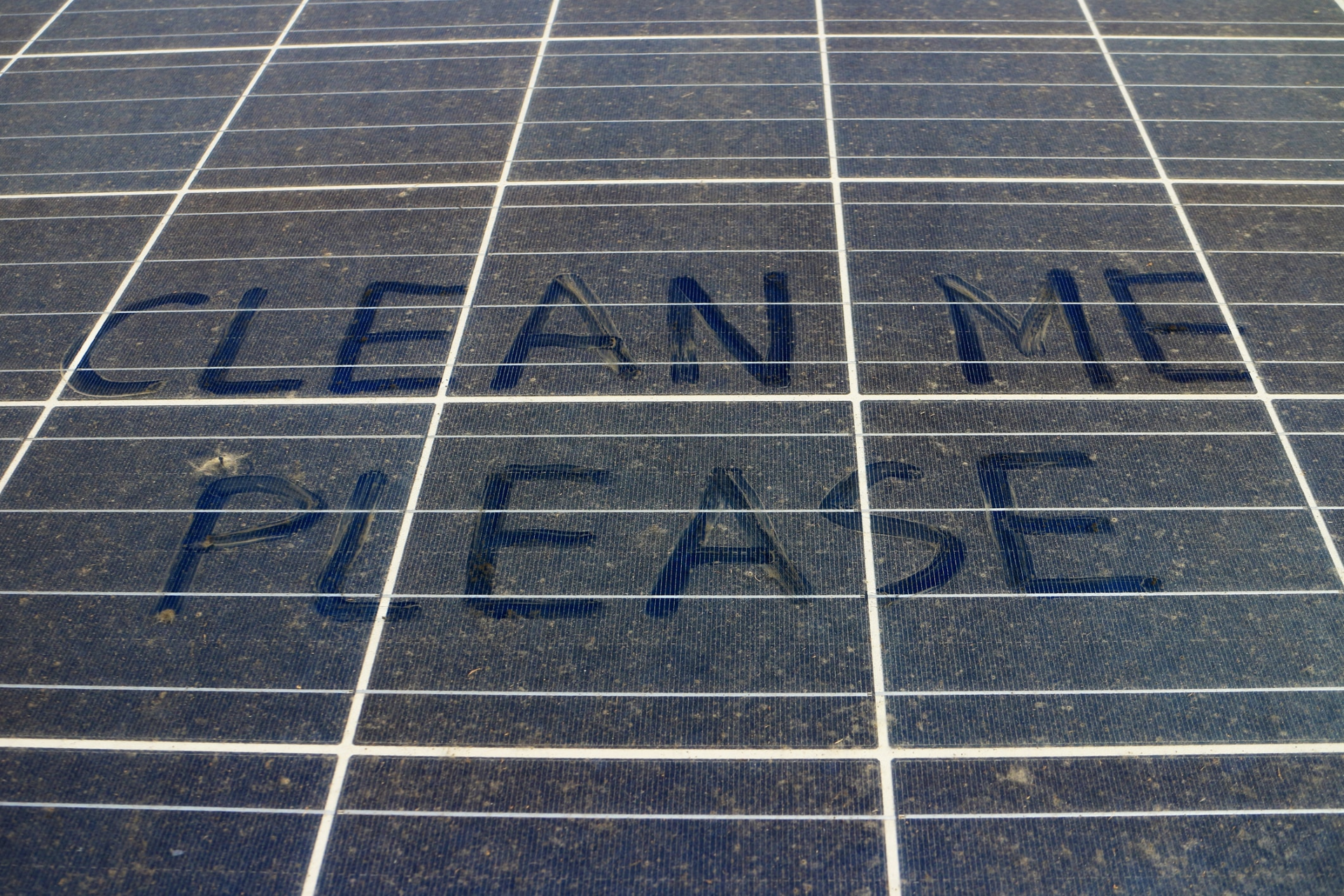
Bombardier case study
Project Summary
A multinational manufacturer of business jets and rail – Bombardier – commissioned Jigsaw Business Group to conduct a value stream review, to verify data and, recommend and implement improvements to its 2-shift Bogey re-manufacturing operation at its Crewe manufacturing plant. From the review process the company made a series of recommendations that significantly enhanced the re-manufacturing process.
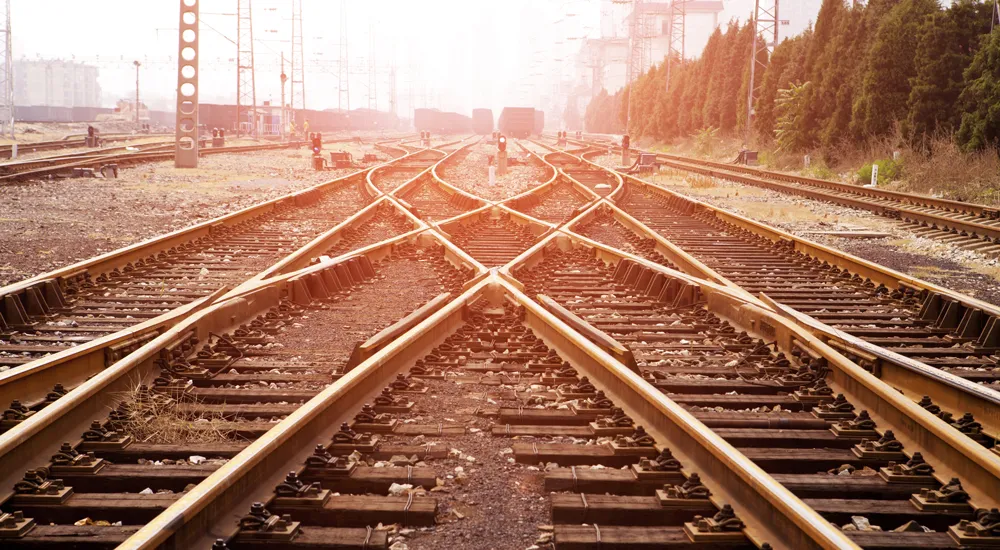
The Challenge
- Under new management, Bombardier required an analysis of its rail rolling-stock bogeys being re-manufactured at its Crewe facilities;
- The company wanted to engage with a specialist that would be able to analyse the operation and recommend improvements to significantly improve efficiencies of the remanufacturing operations.
The Solution
- Jigsaw Business Group produced value stream maps – lean-management method for analysing the current and future design state – for the bogey strip and rebuild operations;
- The company further conducted time studies across both shifts observing the following:
- Different methods/times on each shift;
- Batch building with significant bottlenecks;
- No performance monitoring – no production smoothing;
- Significant losses in waiting time;
- Poor workflow and housekeeping.
Why Jigsaw Business Group?
- A proven track record with a team possessing real industry experience with empathy to support businesses accordingly, understanding individual pain points;
- Unrivalled sector knowledge and technical expertise with an ability to look at things from a fresh perspective to deliver process driven solutions that help businesses to reduce costs, increase efficiencies and streamline business operations;
- A progressive company delivering premium level support services working in strict adherence with robust in-house best practices in accordance with all industry standards.
Key Achievements
Jigsaw Business Group successfully:
- Implemented Standard Operating Procedures (SOP) on both shifts;
- Implemented second turnover station and other layout changes to eliminate bottlenecks;
- Implemented QA schedule to remove waiting time;
- Introduced a method to produce all bogeys on a single shift with a headcount of 18 (initial headcount across 2 shifts = 39).
- Under new management, Bombardier required an analysis of its rail rolling-stock bogeys being re-manufactured at its Crewe facilities;
- The company wanted to engage with a specialist that would be able to analyse the operation and recommend improvements to significantly improve efficiencies of the remanufacturing operations.
- Jigsaw Business Group produced value stream maps – lean-management method for analysing the current and future design state – for the bogey strip and rebuild operations;
- The company further conducted time studies across both shifts observing the following:
- Different methods/times on each shift;
- Batch building with significant bottlenecks;
- No performance monitoring – no production smoothing;
- Significant losses in waiting time;
- Poor workflow and housekeeping.
- A proven track record with a team possessing real industry experience with empathy to support businesses accordingly, understanding individual pain points;
- Unrivalled sector knowledge and technical expertise with an ability to look at things from a fresh perspective to deliver process driven solutions that help businesses to reduce costs, increase efficiencies and streamline business operations;
- A progressive company delivering premium level support services working in strict adherence with robust in-house best practices in accordance with all industry standards.
Jigsaw Business Group successfully:
- Implemented Standard Operating Procedures (SOP) on both shifts;
- Implemented second turnover station and other layout changes to eliminate bottlenecks;
- Implemented QA schedule to remove waiting time;
- Introduced a method to produce all bogeys on a single shift with a headcount of 18 (initial headcount across 2 shifts = 39).