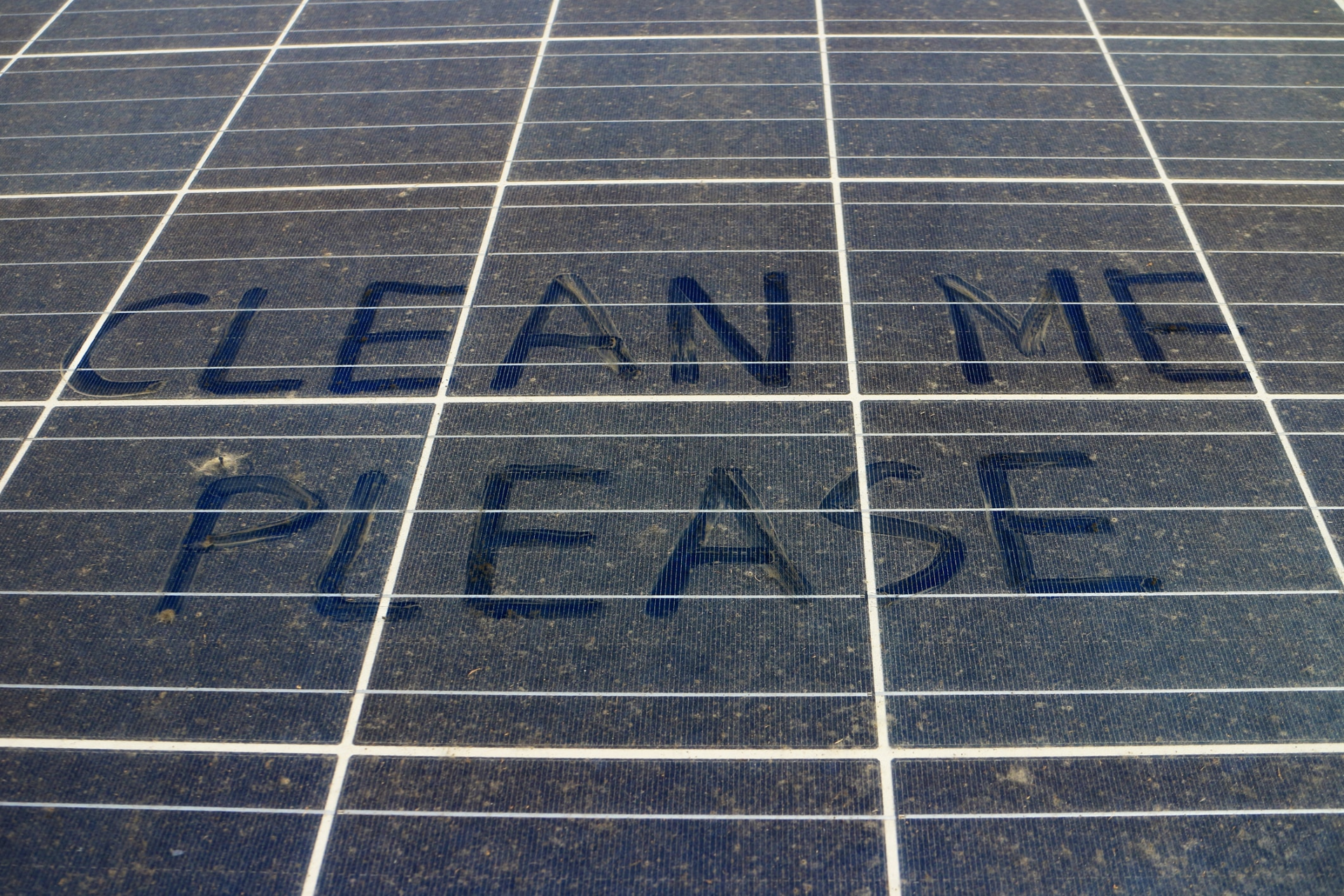
JCB case study
Project Summary
JCB, is a manufacturer of equipment for construction, agriculture, waste handling, and demolition and required from Jigsaw Business Group the transfer of an entire heavy products production facility to a new greenfield site.
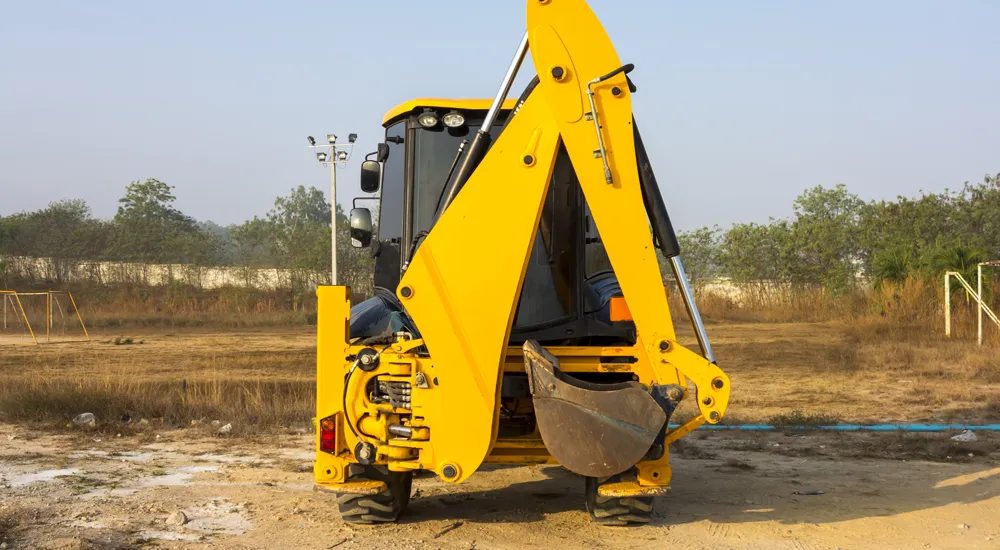
The Challenge
- To manage the entire transfer project end to end;
- To design a new lean takt-based manufacturing and assembly facility along with a pull system supply chain;
- To increase capacity by a factor of three whilst integrating new equipment with refurbished;
- To introduce takt based production to a workforce used to batch manufacture;
- Added complications caused by a delay in the finalisation of the plant specification.
The Solution
- Within the first month, Jigsaw Business Group prepared an extensive, critical path driven project plan including required resources;
- Through a network of suitably qualified interims, Jigsaw Business Group sourced and managed all resources not supplied by the client;
- Jigsaw Business Group managed the integration of the individual projects that made up the overall programme, micro-managing as required to recover any critical slippage;
- Lean manufacturing was introduced as a matter of course across the existing workforce and all support services.
Why Jigsaw Business Group?
- A proven track record with a team possessing real industry experience, as such, possessing empathy to support businesses accordingly, understanding individual pain points.
- Access to an impressive pool of STEM practitioners across the UK and further afield that are ready to be deployed;
- Unrivalled sector knowledge and technical expertise with an ability to look at things from a fresh perspective to deliver process driven solutions that help businesses to reduce costs, increase efficiencies and streamline business operations;
- A progressive company delivering premium level support services working in strict adherence with robust in-house best practices in accordance with all industry standards.
Key Achievements
Despite the complexity of the project and the time restraints, the work was completed on time and under budget.
- To manage the entire transfer project end to end;
- To design a new lean takt-based manufacturing and assembly facility along with a pull system supply chain;
- To increase capacity by a factor of three whilst integrating new equipment with refurbished;
- To introduce takt based production to a workforce used to batch manufacture;
- Added complications caused by a delay in the finalisation of the plant specification.
- Within the first month, Jigsaw Business Group prepared an extensive, critical path driven project plan including required resources;
- Through a network of suitably qualified interims, Jigsaw Business Group sourced and managed all resources not supplied by the client;
- Jigsaw Business Group managed the integration of the individual projects that made up the overall programme, micro-managing as required to recover any critical slippage;
- Lean manufacturing was introduced as a matter of course across the existing workforce and all support services.
- A proven track record with a team possessing real industry experience, as such, possessing empathy to support businesses accordingly, understanding individual pain points.
- Access to an impressive pool of STEM practitioners across the UK and further afield that are ready to be deployed;
- Unrivalled sector knowledge and technical expertise with an ability to look at things from a fresh perspective to deliver process driven solutions that help businesses to reduce costs, increase efficiencies and streamline business operations;
- A progressive company delivering premium level support services working in strict adherence with robust in-house best practices in accordance with all industry standards.
Despite the complexity of the project and the time restraints, the work was completed on time and under budget.