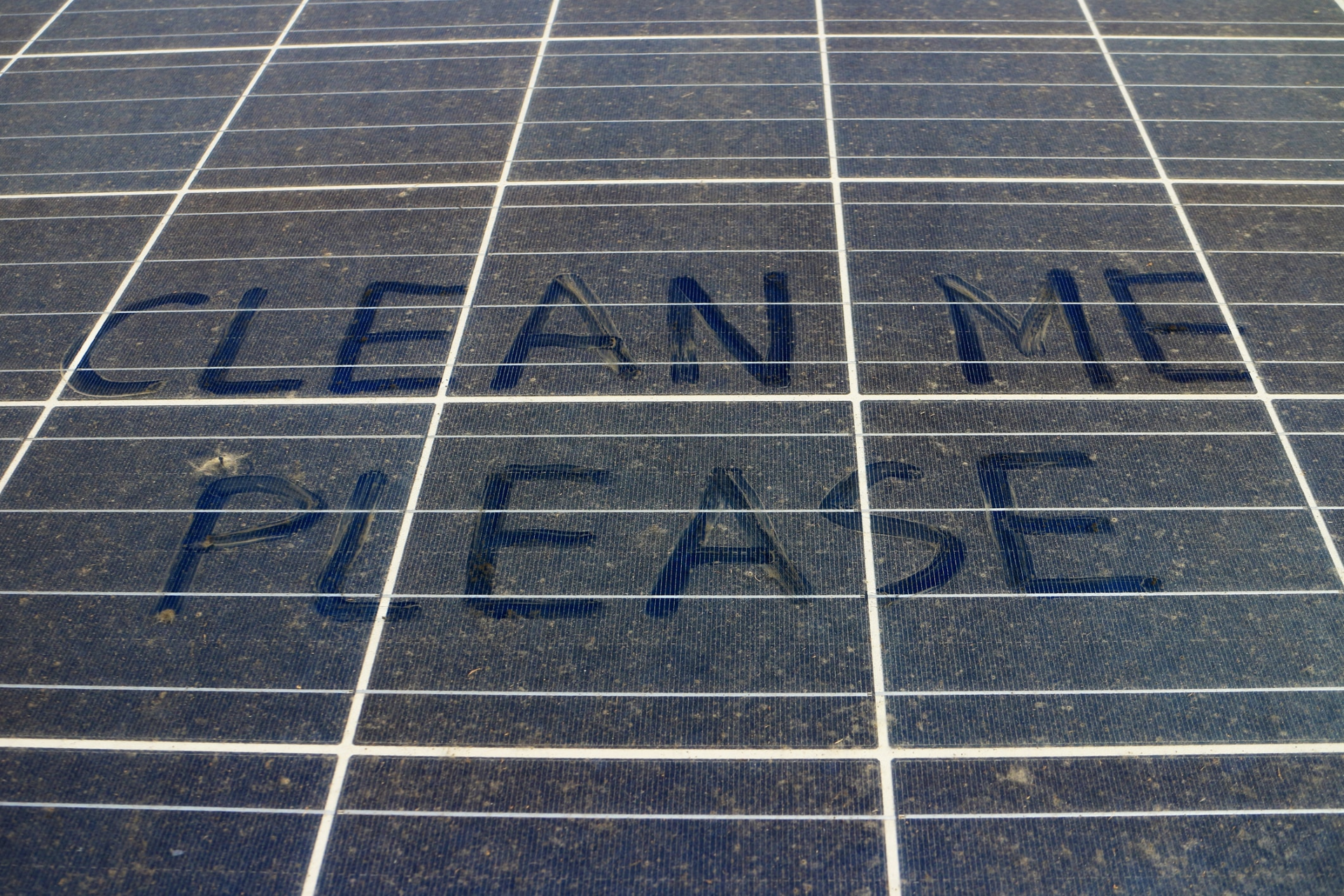
Yunex Traffic case study
Project Summary
Product: Traffic management systems, Electronics
Service: Stock optimisation – PCBs
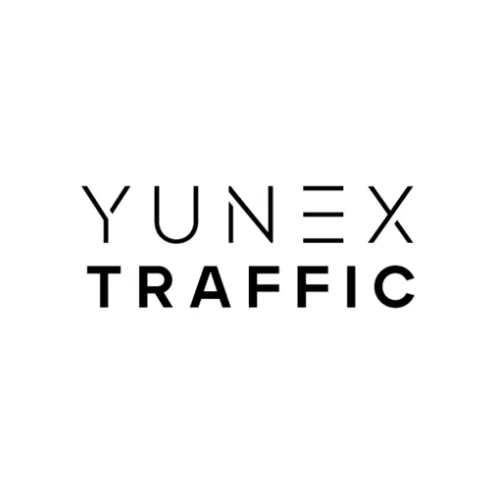
The Challenge
- Yunex Traffic in Poole, UK has been separated in 2022 from Siemens and became an independent Ltd company
- Component crisis since 2020 brought significant changes in stock holding and delivery patterns
- Stock levels of PCBs are doubled since component crisis started – Sept 21
- Yunex asked Jigsaw to help identify the root cause of the inflated stock and review their own internal SIOP process to recommend improvements
The Solution
- Jigsaw provided two experts in supply chain, material planning and logistics and conducted an in-depth study of Yunex’ ordering and supply process.
- Areas of study included forecasting, customers’ orders, suppliers’ orders, ERP, manufacturing and dispatch
- The data was compared to best-case stockholding practices and then worked backward to derive targets for stockholding at Yunex
- SIOP process analysed and contrasted with best-fit process to identify actions
Why Jigsaw Business Group?
- A proven track record with a team possessing real industry experience, as such, possessing empathy to support businesses accordingly, understanding individual pain points.
- Unrivalled sector knowledge and technical expertise with an ability to look at things from a fresh perspective to deliver process driven solutions that help businesses to reduce costs, increase efficiencies and streamline business operations;
Key Achievements
- List of prioritised workstreams to reduce stock by 62%
- Mapped out best-fit SIOP process, including training plan
- Expected customer benefit £250k per year
- Yunex Traffic in Poole, UK has been separated in 2022 from Siemens and became an independent Ltd company
- Component crisis since 2020 brought significant changes in stock holding and delivery patterns
- Stock levels of PCBs are doubled since component crisis started – Sept 21
- Yunex asked Jigsaw to help identify the root cause of the inflated stock and review their own internal SIOP process to recommend improvements
- Jigsaw provided two experts in supply chain, material planning and logistics and conducted an in-depth study of Yunex’ ordering and supply process.
- Areas of study included forecasting, customers’ orders, suppliers’ orders, ERP, manufacturing and dispatch
- The data was compared to best-case stockholding practices and then worked backward to derive targets for stockholding at Yunex
- SIOP process analysed and contrasted with best-fit process to identify actions
- A proven track record with a team possessing real industry experience, as such, possessing empathy to support businesses accordingly, understanding individual pain points.
- Unrivalled sector knowledge and technical expertise with an ability to look at things from a fresh perspective to deliver process driven solutions that help businesses to reduce costs, increase efficiencies and streamline business operations;
- List of prioritised workstreams to reduce stock by 62%
- Mapped out best-fit SIOP process, including training plan
- Expected customer benefit £250k per year