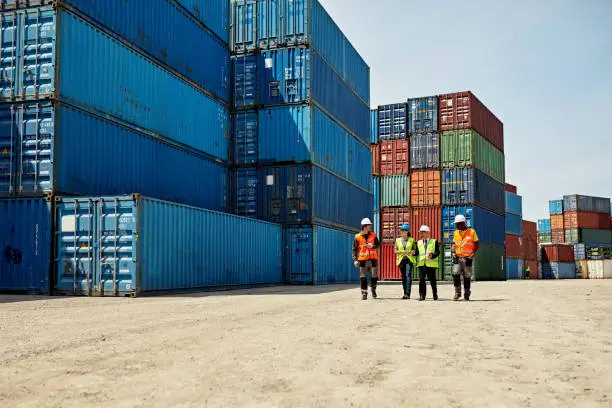
Applied Component Technology (ACT) case study
Project Summary
Applied Component Technology (ACT) – a leading UK automotive parts manufacturer – was looking to launch a new lightweight aircraft galley cart into the aerospace industry. With no prior experience in this sector, the company required external specialist support to develop the new design within only a matter of seven months, overcoming several challenges. Jigsaw Business Group deployed its leading business improvement and supply chain services to support with the delivery of the project, which was achieved on time and, under budget. The project led to the companies scooping top industry accolades in recognition of its innovation.
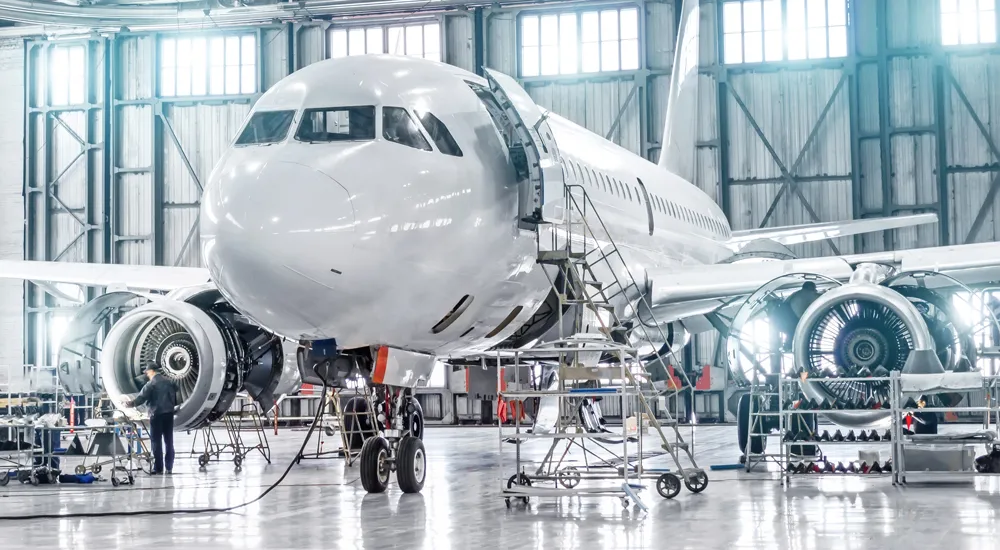
The Challenge
- Jigsaw Business Group was approached by Applied Component Technology (ACT) to support the launch of a totally new design lightweight aircraft galley cart;
- This new product had to be completed within only seven months to be launched at the Hamburg Air-show;
- In addition to the timing challenges the product used new materials which had not been previously used for such applications;
- ACTs development and manufacturing experience did not include the Aerospace industry;
- The short development time, limited budget and resource constraints of ACT meant without external support there was no chance to deliver this accelerated development project.
The Solution
- Jigsaw Business Group provided core resources which, together with ACT team members, formed an integrated, collocated project team;
- The company provided programme management, launch, purchasing and quality support, as well as production management;
- The project called for immediate concept review, re-design to suit targets, cost base and employing lessons learnt from the automotive experience of both businesses;
- Key tools used in product design included DFMEA, QFD & APQP and to keep plant assembly capital cost and expenditure to a minimum, DFM techniques were deployed.;
- The supply base was also revamped to bring in expertise from the Aerospace industries.
Why Jigsaw Business Group?
- A proven track record with a team possessing real industry experience with empathy to support businesses accordingly, understanding individual pain points;
- Access to an impressive pool of STEM practitioners across the UK and further afield that are ready to be deployed;
- Unrivalled sector knowledge and technical expertise with an ability to look at things from a fresh perspective to deliver process driven solutions that help businesses to reduce costs, increase efficiencies and streamline business operations;
- A progressive company delivering premium level support services working in strict adherence with robust in-house best practices in accordance with all industry standards.
Key Achievements
- The teamwork resulted in achieving all technical and commercial targets within the seven months development programme;
- The product was successfully tested and launched at the Hamburg Air-show as required;
- The work with the supply base delivered a significantly reduced cost BOM (>30%);
- Despite introducing a high quality, fully traceable, ‘no-fault-forward’ automated production line to suit volumes of c. 60,000 p.a. and new presses for composite production, total capex was less held at than £500k.
The impact of this innovative work was recognised with a number of awards including:
EEF/Aldermore Future Manufacturing National Awards
- Gold Prize – Smart Product Awards
EEF Future Manufacturers Regional Awards
- EEF NW Gold – Environmental Efficiency Award
- EEF NW Gold – Smart Product Award
- EEF NE Silver – Environmental Efficiency Award.
- Jigsaw Business Group was approached by Applied Component Technology (ACT) to support the launch of a totally new design lightweight aircraft galley cart;
- This new product had to be completed within only seven months to be launched at the Hamburg Air-show;
- In addition to the timing challenges the product used new materials which had not been previously used for such applications;
- ACTs development and manufacturing experience did not include the Aerospace industry;
- The short development time, limited budget and resource constraints of ACT meant without external support there was no chance to deliver this accelerated development project.
- Jigsaw Business Group provided core resources which, together with ACT team members, formed an integrated, collocated project team;
- The company provided programme management, launch, purchasing and quality support, as well as production management;
- The project called for immediate concept review, re-design to suit targets, cost base and employing lessons learnt from the automotive experience of both businesses;
- Key tools used in product design included DFMEA, QFD & APQP and to keep plant assembly capital cost and expenditure to a minimum, DFM techniques were deployed.;
- The supply base was also revamped to bring in expertise from the Aerospace industries.
- A proven track record with a team possessing real industry experience with empathy to support businesses accordingly, understanding individual pain points;
- Access to an impressive pool of STEM practitioners across the UK and further afield that are ready to be deployed;
- Unrivalled sector knowledge and technical expertise with an ability to look at things from a fresh perspective to deliver process driven solutions that help businesses to reduce costs, increase efficiencies and streamline business operations;
- A progressive company delivering premium level support services working in strict adherence with robust in-house best practices in accordance with all industry standards.
- The teamwork resulted in achieving all technical and commercial targets within the seven months development programme;
- The product was successfully tested and launched at the Hamburg Air-show as required;
- The work with the supply base delivered a significantly reduced cost BOM (>30%);
- Despite introducing a high quality, fully traceable, ‘no-fault-forward’ automated production line to suit volumes of c. 60,000 p.a. and new presses for composite production, total capex was less held at than £500k.
The impact of this innovative work was recognised with a number of awards including:
EEF/Aldermore Future Manufacturing National Awards
- Gold Prize – Smart Product Awards
EEF Future Manufacturers Regional Awards
- EEF NW Gold – Environmental Efficiency Award
- EEF NW Gold – Smart Product Award
- EEF NE Silver – Environmental Efficiency Award.