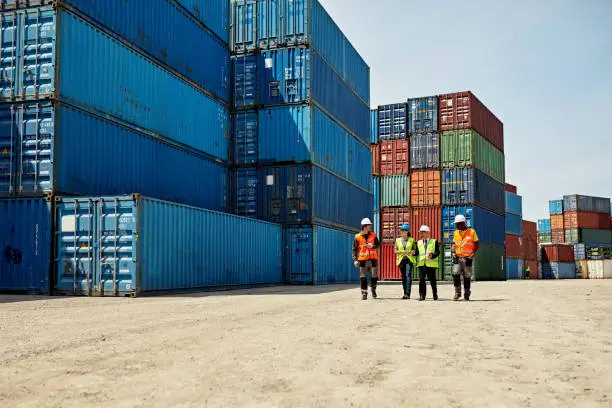
Pandora case study
Project Summary
Pandora, which had grown exponentially from an independent retailer to a globally recognised jewellery brand, needed support on global quality issues whilst embedding appropriate operating systems and processes.
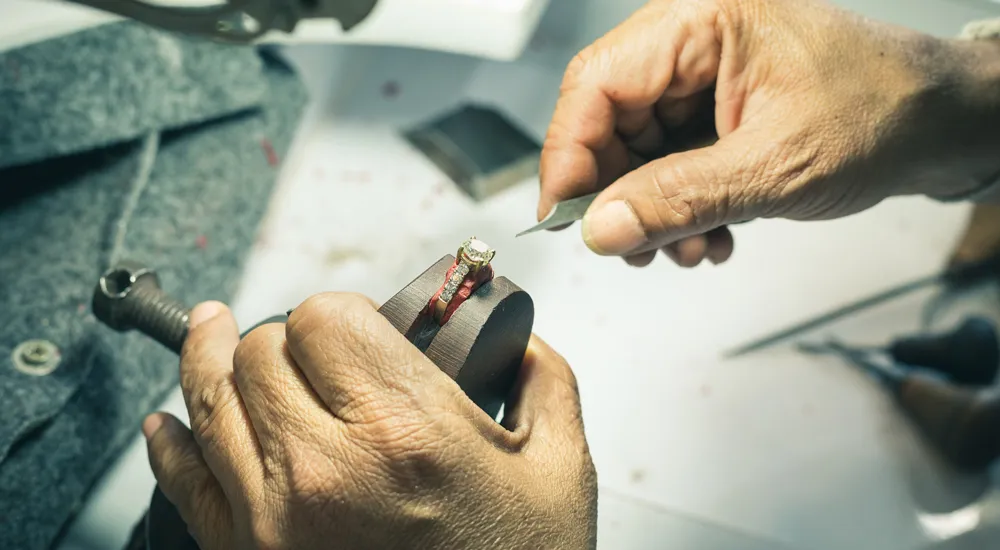
The Challenge
- The requirement to find a solution that would fix persistent quality issues whilst also reviewing and advising on global quality operating processes and quality aspirations;
- Taking automotive best practice quality tools and applying them to an industry with a completely different mindset and definition of Quality.
The Solution
- Jigsaw Business Group established a team of International Quality Assurance experts to identify company and industry practices that could be enhanced by the application of proven automotive quality assurance tools and disciplines;
- Project activities were spread across several regions – Europe, Asia, US and deployed across local practitioners;
- Jigsaw Business Group worked across the entire Pandora supply chain to demonstrate how quality is impacted across this;
- The deployment of clear and robust policy and governance frameworks; the inclusion of lessons learned feedback to design function DFMEA; the deployment of a structured NPD/NPI calendar and company wide use of standard problem-solving techniques, such as 8D;
- The deployment of key local experts: a design expert from Germany, a Problem-Solving expert in the US and a Quality Auditor in Thailand;
- Due care and practical techniques used to ensure the client was brought with us on every step of the journey from Quality Control to Quality Assurance.
Why Jigsaw Business Group?
- A proven track record with a team possessing real industry experience, as such, possessing empathy to support businesses accordingly, understanding individual pain points.
- Unrivalled sector knowledge and technical expertise with an ability to look at things from a fresh perspective to deliver process driven solutions that help businesses to reduce costs, increase efficiencies and streamline business operations;
- A progressive company delivering premium level support services working in strict adherence with robust in-house best practices in accordance with all industry standards.
Key Achievements
- The root cause of the main defect was identified and countermeasures implemented;
- Of the 11 changes proposed by Jigsaw, ten were adopted and implemented by Pandora and proved to have a significant positive impact on product quality, cost and timing;
- An additional scope item – a Product Recall Process – was designed and developed by Jigsaw and is now fully implemented by Pandora;
- Processes and policies were implemented, making the client self-sufficient in their strive for product quality.
- The requirement to find a solution that would fix persistent quality issues whilst also reviewing and advising on global quality operating processes and quality aspirations;
- Taking automotive best practice quality tools and applying them to an industry with a completely different mindset and definition of Quality.
- Jigsaw Business Group established a team of International Quality Assurance experts to identify company and industry practices that could be enhanced by the application of proven automotive quality assurance tools and disciplines;
- Project activities were spread across several regions – Europe, Asia, US and deployed across local practitioners;
- Jigsaw Business Group worked across the entire Pandora supply chain to demonstrate how quality is impacted across this;
- The deployment of clear and robust policy and governance frameworks; the inclusion of lessons learned feedback to design function DFMEA; the deployment of a structured NPD/NPI calendar and company wide use of standard problem-solving techniques, such as 8D;
- The deployment of key local experts: a design expert from Germany, a Problem-Solving expert in the US and a Quality Auditor in Thailand;
- Due care and practical techniques used to ensure the client was brought with us on every step of the journey from Quality Control to Quality Assurance.
- A proven track record with a team possessing real industry experience, as such, possessing empathy to support businesses accordingly, understanding individual pain points.
- Unrivalled sector knowledge and technical expertise with an ability to look at things from a fresh perspective to deliver process driven solutions that help businesses to reduce costs, increase efficiencies and streamline business operations;
- A progressive company delivering premium level support services working in strict adherence with robust in-house best practices in accordance with all industry standards.
- The root cause of the main defect was identified and countermeasures implemented;
- Of the 11 changes proposed by Jigsaw, ten were adopted and implemented by Pandora and proved to have a significant positive impact on product quality, cost and timing;
- An additional scope item – a Product Recall Process – was designed and developed by Jigsaw and is now fully implemented by Pandora;
- Processes and policies were implemented, making the client self-sufficient in their strive for product quality.